What Is an Automated Warehouse and Should You Invest in One?
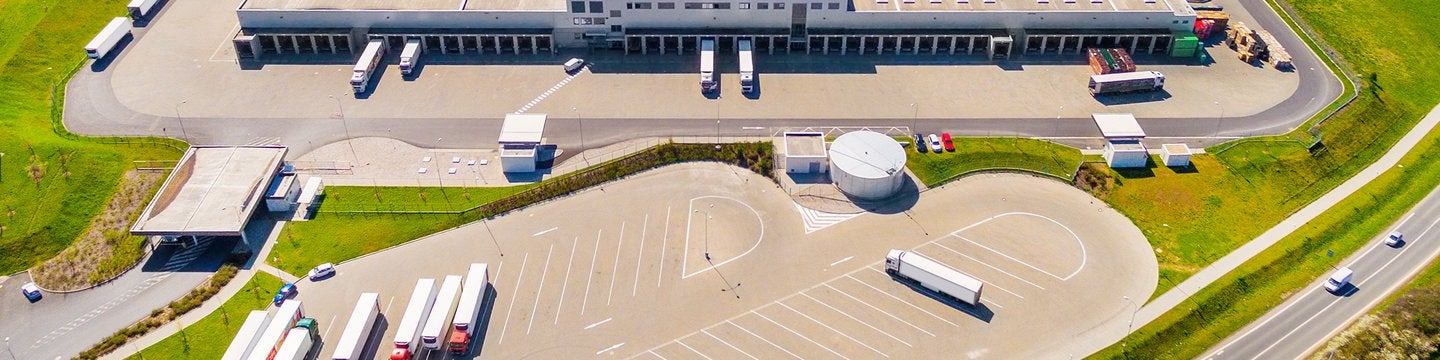
Like most industries in our technological era, industrial real estate is making big moves into the 21st century. Automated warehouses, one of the newest technological trends in this commercial real estate (CRE) sector, have become a high-demand asset among the fulfillment, materials handling, logistics, and supply-chain industries.
By utilizing technology to improve and automate systems, tasks, and jobs that traditionally would be completed by workers, an automated warehouse improves operational efficiency and reduces overhead and liability while aiding in marketplace competitiveness. Automated warehouses may sound like something from the future but are becoming a very real and sought- after solution in the warehouse and logistics sector today. Learn how automated warehouses work, where the industry is headed, and ultimately if automated warehousing is a worthwhile investment for the long term.
How is a warehouse automated?
Automated warehouses can be newly developed industrial warehouses or distribution centers that utilize new state-of-the-art technology and building specifications or older buildings that integrate new automation systems and softwares to the existing warehouse. What truly classifies a warehouse as automated is the warehouse automation system, which can include:
- Automated storage and retrieval system (ASRS), which can include drone, automated forklift, robotics, conveyor, or light systems to improve the process of retrieving, packaging, or organizing inventory for storage, order fulfillment, or delivery.
- Application programming interfaces (APIs), which communicate with the software to communicate with the various information systems.
- Cloud computing and data analytics that can provide predictions about inventory supply and demand or cartonization suggestions helping pick the right box size based on the item’s dimensions and weight.
- Radio-frequency identification (RFID) to provide real-time tracking of inventory and warehouse operations, including inventory management (this is how Amazon (NASDAQ: AMZN) Go is able to detect what you pick up and actually buy without any human interaction).
Benefits of warehouse automation
Warehouse automation technology is used across multiple subsectors of industrial real estate to improve speed in order fulfillment and shipping, reduce employee liability and fatigue, eliminate common human errors in manual warehouses, more accurately monitor and maintain operations and inventory, reduce expenses, and improve warehouse efficiency as a whole.
Drawbacks of warehouse automation
An automated warehouse system is not cheap; installing automated equipment, systems, and software is a big up-front expense for existing warehouse operators and requires careful forethought and capital among new developments. While the up-front, initial cost can be steep, the high cost is quickly made up for through expense savings and improved efficiency, which allows for a warehouse manager to scale their business and increase revenues. Another drawback is the perpetual advancement of technology. Even if you’re installing the newest and best automation solution, chances are a new development will replace or improve that solution in the near future.
Not enough supply to meet demand
Many warehouse operators have started to integrate some of these technologies to improve their automated systems in today’s warehouses, but there aren’t nearly enough existing automated facilities to meet current demand. Cold storage is one sector in particular that saw a recent surge in demand as a result of the coronavirus pandemic. Supply-chain interruptions and increased online grocery shopping have created a high appetite for newly developed automated warehouses that provide the state of the art technology.
Bob West, Director of Industrial Business Development for Ryan Companies, said in email correspondence, “We’re drinking from a fire hose right now.” Ryan, which has designed and constructed multiple projects for Amazon and currently one of the leading builders for the world’s largest retailer, has completed 40 automated warehouse projects (33+ million square feet) in 20 states for leading brands such as Kroger (NYSE: KR), Target (NYSE: TGT), and Nestle Purina, among others.
“Speed to market was essential for Kroger given the rapid development of events impacting the supply chain, but the level of sophistication required on the design and construction side to accommodate all of the advanced robotics and technology that will be deployed is still somewhat limited in our industry as a whole,” said West. “More than 4 million robots are expected to be installed in 50,000 warehouses by 2025, compared to just 4,000 two years ago. The e-commerce arms race you’re seeing among grocers is certainly causing an acceleration in automated warehouse service offerings among industrial developers and builders, and those who can provide a comprehensive menu under one roof will be in the driver’s seat.”
How to invest in automated warehouses
The easiest way for investors to participate in the potential of warehouse automation is by investing in industrial real estate investment trusts (REITs) that are currently developing or installing automated warehouse technology. Americold Realty Trust (NYSE: COLD) is the only publicly traded cold-storage warehouse, distribution, and logistics company that is vastly expanding its market reach. Many of their facilities utilize warehouse automation solutions to compete in the marketplace and help with tenant retention.
Private hedge funds and crowdfunding opportunities are also a potential avenue to explore. It’s important, however, to do your due diligence on each company, sponsor, and the particular investment at hand before investing. Just because a market is ripe with opportunity does not mean every investment holds as much opportunity or potential. Market conditions, warehouse fatigue, and risk of oversupply in certain markets as development ramps up are all realistic problems that could confront the industrial sector in over the next decade.
Real estate investors who may currently own an industrial building can try to install or integrate a warehouse automation solution to compete in the marketplace.
The trend of the future
There’s no doubt Amazon is leading the way for the warehouse-automation market with several of its subsidiary companies like Zappos and Diapers.com utilizing warehouse automations already. But other mega retailers, like Ikea, Nike (NYSE: NKE), and UPS (NYSE: UPS) are following suit.
A recent study by CBRE Group (NYSE: CBRE) found that the industrial sector is expected to have an annual net absorption of more than 333 million sq. ft. by 2022, leading to annual rent growth of 5.7%. Those who integrate the latest state-of-the art technology will help compete and achieve higher rents than those who don’t. It’s not a question of whether this trend will last; it’s a question of how quickly the industrial market will adapt to the current demand.
11% of the mega-wealthy swear by this investment…
The richest in the world have made their fortunes in many ways, but there is one common thread for many of them: They made real estate a core part of their investment strategy. Of all the ways the ultra-rich made their fortunes, real estate outpaced every other method 3 to 1.
If you, too, want to invest like the wealthiest in the world, we have a complete guide on what you need to take your first steps. Take the first step toward building real wealth by getting your free copy today. Simply click here to receive your free guide.